Hyundai Palisade: ESP(Electronic Stability Program) System / Troubleshooting
1. |
In principle, ESP and TCS controls are prohibited in case of ABS failure.
|
2. |
When ESP or TCS fails, only the failed system control is prohibited.
|
3. |
However, when the solenoid valve relay should be turned off in case
of ESP failure, refer to the ABS fail-safe.
|
4. |
Information on ABS fail-safe is identical to the fail-safe in systems
where ESP is not installed.
|
Memory of Fail Code
1. |
It keeps the code as far as the backup lamp power is connected. (O)
|
2. |
It keeps the code as far as the HCU power is on. (X)
|
Failure Checkup
1. |
Initial checkup is performed immediately after the HECU power on.
|
2. |
Valve relay checkup is performed immediately after the IG2 ON.
|
3. |
It executes the checkup all the time while the IG2 power is on.
|
Countermeasures in Fail
1. |
Turn the system down and perform the following actions and wait for
HECU power OFF.
|
2. |
Turn the valve relay off.
|
3. |
Stop the control during the operation and do not execute any until the
normal condition recovers.
|
Warning Lamp ON
1. |
ESP warning lamp turn on for 3sec after IGN ON.
|
2. |
ESP function lamp blinks when ESP Act.
|
3. |
If ESP fail occured, ESP warning turns ON.
|
4. |
ESP OFF lamp turn on in case of
|
Standard Flow of Diagnostic Troubleshooting
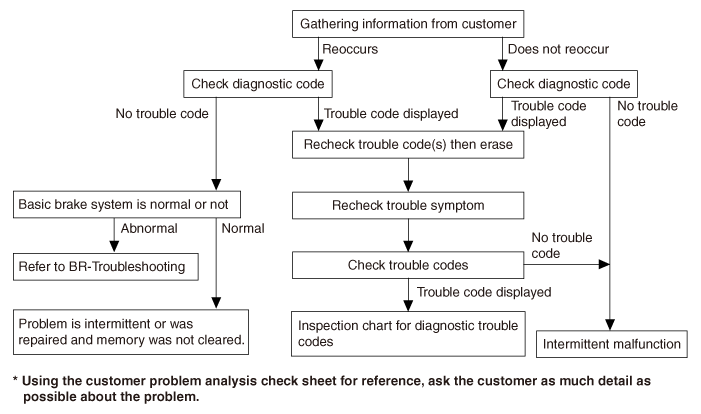
Notes With Regard to Diagnosis
The phenomena listed in the following table are not abnormal.
Condition
|
Explanation
|
System check sound
|
When starting the engine, a thudding sound can sometimes be heard coming
from inside the engine compartment. This is because the system operation
check is being performed.
|
ABS operation sound
|
1) |
Sound of the motor inside the ABS hydraulic unit operation (whine).
|
2) |
Sound is generated along with vibration of the brake pedal (scraping).
|
3) |
When ABS operates, sound is generated from the vehicle chassis
due to repeated brake application and release (Thump : suspension;
squeak : tires)
|
|
ABS operation (Long braking distance)
|
For road surfaces such as snow-covered and gravel roads, the braking distance
for vehicles with ABS can sometimes be longer than that for other vehicles.
Accordingly, advise the customer to drive safely on such roads by lowering
the vehicle speed.
|
Inspection method
With the IGN OFF, set the IGN to ON position : If the ABS/Brake Warning Light
illuminates and distinguishes after 3 seconds, the warning lamp and ABS system
are all normal.
1. |
If the Warning Light does not illuminate when IGN is set to ON position
(1) |
Remove the ABS ECU connecter (located in the engine room).
|
(2) |
Set the IGN to ON position.
|
(3) |
If the ABS/Brake Warning Light does not illuminate: The failure
is related to the Warning Light. Check the instrument cluster
and wiring.
|
(4) |
If the ABS/Brake Warning Light illuminates and stays on :
|
The Warning Light is normal and judged to be failure of the VDC system.
Inspect the VDC system using GDS.
|
2. |
If the Warning Light does not distinguish after its illumination when
IGN is set to ON position.
(1) |
Self-diagnose using GDS.
|
(3) |
Self-diagnose after erasing the fault code.
|
(4) |
If the result of self-diagnosis is normal after erasing the
fault code :
Set the IGN to OFF, then to ON position and check whether the
Warning Light operates normally.
|
(5) |
If the result of self-diagnosis continues to display error after
erasing the fault code :
Check according to the inspection sheet of the fault code.
|
|
3. |
Even if the Warning Light and VDC system are all normal, erase all the
memorized fault codes using GDS (if there is no memorized fault code,
record the fault code).
1) |
When removing or engaging all the connectors set the
IGN to OFF position.
|
2) |
During the driving test, record on the inspection sheet
when the Warning Light illuminates or every time any
event is occurred.
|
|
|
ABS Check Sheet
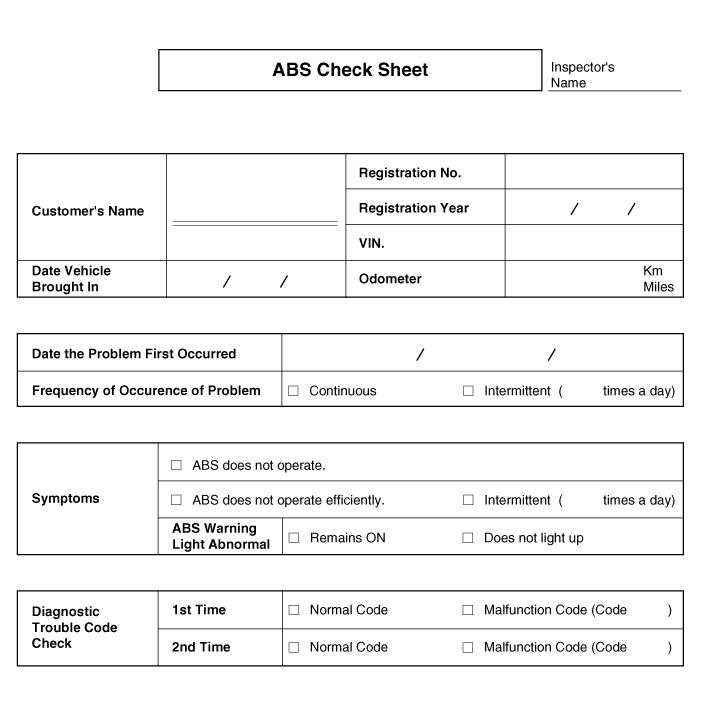
Problem Symptoms Table
Symptom
|
Suspect Area
|
ABS does not operate.
|
Only when 1 - 4 are all normal and the problem is still occurring, replace
the HECU.
1) |
Check the DTC reconfirming that the normal code is output.
|
4) |
Check the hydraulic circuit for leakage.
|
|
ABS does not operate intermittently.
|
Only when 1 - 4 are all normal and the problem is still occurring, replace
the ABS actuator assembly.
1) |
Check the DTC reconfirming that the normal code is output.
|
2) |
Wheel speed sensor circuit.
|
3) |
Stop lamp switch circuit.
|
4) |
Check the hydraulic circuit for leakage.
|
|
Communication with GDS is not possible. (Communication with any system is
not possible)
|
|
Communication with GDS is not possible. (Communication with ABS only is
not possible)
|
|
When ignition key is turned ON (engine OFF), the ABS warning lamp does not
light up.
|
1) |
ABS warning lamp circuit
|
|
Even after the engine is started, the ABS warning lamp remains ON.
|
1) |
ABS warning lamp circuit
|
|
• |
During ABS operation, the brake pedal may vibrate or may not
be able to be depressed. Such phenomena are due to intermittent
changes in hydraulic pressure inside the brake line to prevent
the wheels from locking and is not an abnormality.
|
• |
Such phenomena are due to intermittent changes in hydraulic
pressure inside the brake line to prevent the wheels from locking
and is not an abnormality.
|
|

Detecting condition
Trouble Symptoms
|
Possible Cause
|
Brake operation varies depending on driving conditions and road surface
conditions, so diagnosis can be difficult. However if a normal DTC is displayed,
check the following probable cause. When the problem is still occurring,
replace the ESP control module.
|
– |
Faulty power source circuit
|
– |
Faulty wheel speed sensor circuit
|
– |
Faulty hydraulic circuit for leakage
|
|
Inspection procedures
DTC Inspection
1. |
Connect the GDS with the data link connector and turn the ignition switch
ON.
|
2. |
Verify that the DTC code is output.
|
3. |
Is the DTC code output?

|
▶ Check the power source
circuit.
|

|
▶ Erase the DTC and recheck
using GDS.
|
|
Check the power source circuit
1. |
Disconnect the connector from the ESP control module.
|
2. |
Turn the ignition switch ON, measure the voltage between terminal 29
of the ESP control module harness side connector and body ground.
Specification : approximately B+
|
Is the voltage within specification?

|
▶ Check the ground circuit.
|

|
▶ Check the harness or
connector between the fuse (7.5A) in the engine compartment junction
block and the ESP control module. Repair if necessary.
|
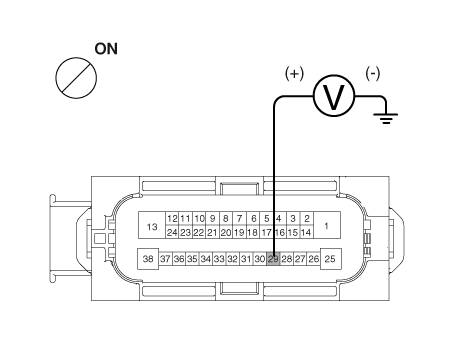
|
Check the ground circuit
1. |
Disconnect the connector from the ESP control module.
|
2. |
Check for continuity between terminals 13, 38 of the ESP control module
harness side connector and ground point.
Is there continuity?

|
▶ Check the wheel speed
sensor circuit.
|

|
▶ Repair an open in the
wire and ground point.
|
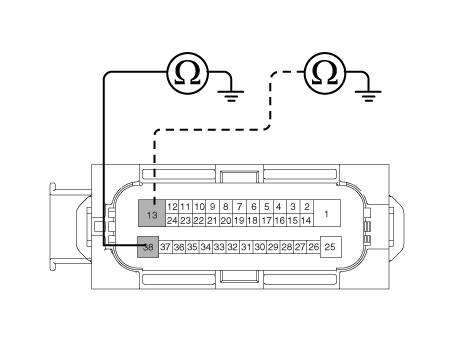
|
Check the wheel speed sensor circuit
1. |
Refer to the DTC troubleshooting procedures.
|
2. |
Is it normal?

|
▶ Check the hydraulic
circuit for leakage.
|

|
▶ Repair or replace the
wheel speed sensor.
|
|
Check the hydraulic circuit for leakage
1. |
Inspect leakage of the hydraulic lines.
|
2. |
Is it normal?

|
▶ The problem is still
occurring, replace the ESP control module.
|

|
▶ Repair the hydraulic
lines for leakage.
|
|

Detecting condition
Trouble Symptoms
|
Possible Cause
|
Brake operation varies depending on driving conditions and road surface
conditions, so diagnosis can be difficult. However if a normal DTC is displayed,
check the following probable cause. When the problem is still occurring,
replace the ESP control module.
|
– |
Faulty power source circuit
|
– |
Faulty wheel speed sensor circuit
|
– |
Faulty hydraulic circuit for leakage
|
|
Inspection procedures
DTC Inspection
1. |
Connect the GDS with the data link connector and turn the ignition switch
ON.
|
2. |
Verify that the DTC code is output.
|
3. |
Is the DTC code output?

|
▶ Check the wheel speed
sensor circuit.
|

|
▶ Erase the DTC and recheck
using GDS.
|
|
Check the wheel speed sensor circuit
1. |
Refer to the DTC troubleshooting procedures.
|
2. |
Is it normal?

|
▶ Check the stop lamp
switch circuit.
|

|
▶ Repair or replace the
wheel speed sensor.
|
|
Check the stop lamp switch circuit
1. |
Check that stop lamp lights up when brake pedal is depressed and turns
off when brake pedal is released.
|
2. |
Measure the voltage between terminal 23 of the ESP control module harness
side connector and body ground when brake pedal is depressed.
Specification : approximately B+
|
Is the voltage within specification?

|
▶ Check the hydraulic
circuit for leakage.
|

|
▶ Repair the stop lamp
switch. Repair an open in the wire between the ESP control module
and the stop lamp switch.
|
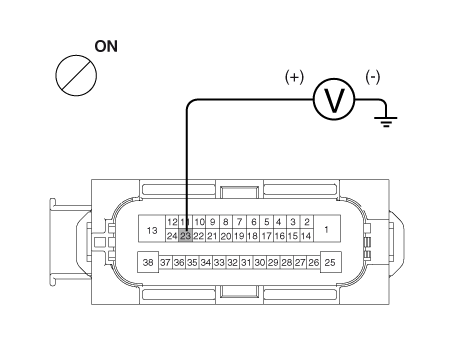
|
Check the hydraulic circuit for leakage
1. |
Refer to the hydraulic lines.
|
2. |
Inspection leakage of the hydraulic lines.
|
3. |
Is it normal?

|
▶ The problem is still
occurring, replace the ESP control module.
|

|
▶ Repair the hydraulic
lines for leakage.
|
|

Detecting condition
Trouble Symptoms
|
Possible Cause
|
Possible defect in the power supply system (including ground) for the diagnosis
line.
|
– |
Faulty power source circuit
|
|
Inspection procedures
Check The Power Supply Circuit For The Diagnosis
1. |
Measure the voltage between terminal 16 of the data link connector and
body ground.
Specification : approximately B+
|
Is voltage within specification?

|
▶ Check the ground circuit
for the diagnosis.
|

|
▶ Repair an open in the
wire. Check and replace fuse from the engine compartment junction
block.
|
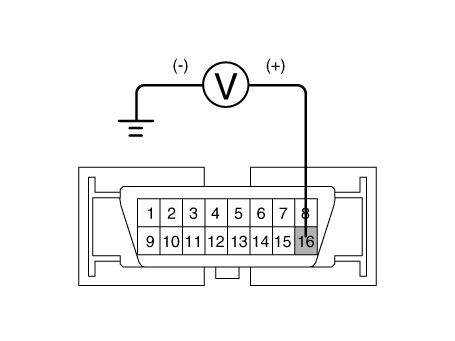
|
Check the ground circuit for the diagnosis
1. |
Check for continuity between terminal 4 of the data link connector and
body ground.
Is there continuity?

|
▶ Repair an open in the
wire between terminal 4 of the data link connector and ground point.
|
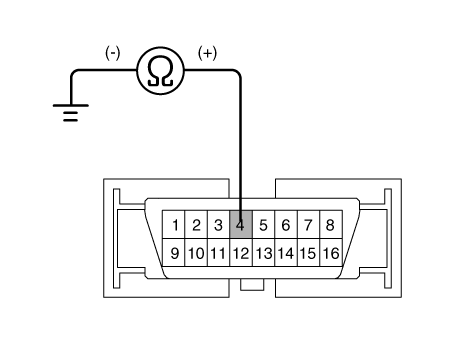
|

Detecting condition
Trouble Symptoms
|
Possible Cause
|
When communication with GDS is not possible, the cause may be probably an
open in the HECU power circuit or an open in the diagnosis output circuit.
|
– |
Faulty power source circuit
|
|
Inspection procedures
Check for Continuity in the CAN Line
1. |
Disconnect the connector from the ESP control module.
|
2. |
Check for continuity between terminals 26, 14 of the ESP control module
connector and 3, 11 of the data link connector.
|
3. |
Is there continuity?

|
▶ Check the power source
of ESP control module.
|

|
▶ Repair an open in the
wire.
|
|
Check the power source of ESP control module
1. |
Disconnect the connector from the ESP control module.
|
2. |
Turn the ignition switch ON, measure the voltage between terminal 29
of the ESP control module harness side connector and body ground.
Specification : approximately B+
|
Is voltage within specification?

|
▶ Check for poor ground.
|

|
▶ Check the harness or
connector between the fuse (10A) in the engine compartment junction
block and the ESP control module.Repair if necessary.
|
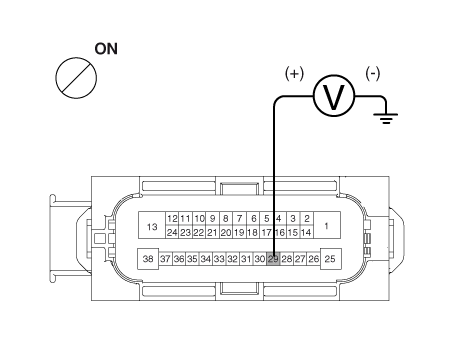
|
Check for poor ground
1. |
Check for continuity between terminal 4 of the data link connector and
ground point.
|
2. |
Is the electric current applied between groundings?

|
▶ Replace the ESP control
module and recheck.
|

|
▶ Repair an open in the
wire or poor ground
|
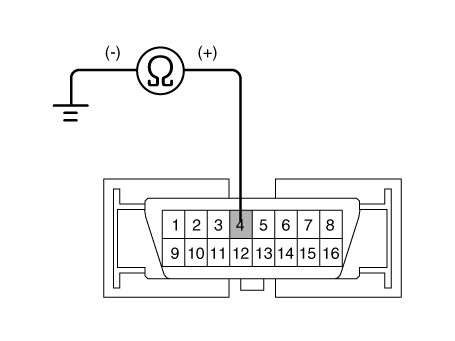
|

Detecting condition
Trouble Symptoms
|
Possible Cause
|
When current flows in the HECU the ABS warning lamp turns from ON to OFF
as the initial check. Therefore if the lamp does not light up, the cause
may be an open in the lamp power supply circuit, a blown bulb, an open in
the both circuits between the ABS warning lamp and the HECU, and the faulty
HECU.
|
– |
Faulty ABS warning lamp bulb
|
– |
Blown fuse is related to ABS in the engine compartment junction
block
|
– |
Faulty ABS warning lamp damaged
|
– |
Faulty ABS warning lamp module
|
|
Inspection procedures
Problem verification
1. |
Disconnect the connector from the ESP control module and turn the ignition
switch ON.
|
2. |
Does the ABS warning lamp light up?

|
▶ Inspectagain after
replacing the ESP HECU.
|

|
▶ Check the power source
for the ABS warning lamp.
|
|
Check the power source for the ABS warning lamp
1. |
Disconnect the instrument cluster connector (M08) and turn the ignition
switch ON.
|
2. |
Measure the voltage between terminal (M08) 39 of the cluster harness
side connector and body ground.
Specification : approximately B+
|
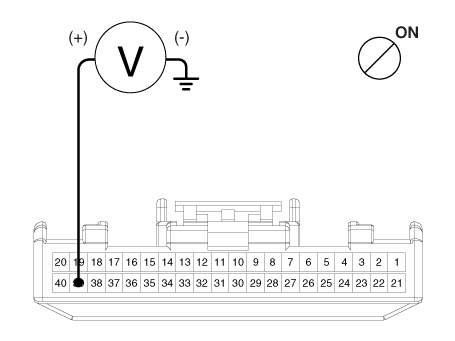
|
3. |
Is voltage within specification?

|
▶ Check the CAN circuit
resistance for ABS warning lamp.
|

|
▶ Check for blown fuse.
|
|
Check the CAN circuit resistance for ABS warning lamp
1. |
Disconnect the instrument cluster connector (M08) and turn the ignition
switch OFF.
|
2. |
Measure the resistance between terminal (M08) 32 and 33 of the cluster
harness side connector.
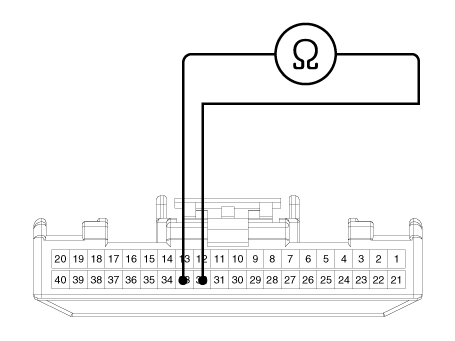
|
3. |
Is resistance within specification?

|
▶ Repair ABS warning
lamp bulb or instrument cluster assembly.
|

|
▶ Check the CAN
circuit wiring for ABS warning lamp.
|
|
Check the CAN circuit wiring for ABS warning lamp
1. |
Disconnect the instrument cluster connector (M08) and ESP HECU connector,
and then turn the ignition switch OFF.
|
2. |
Check for continuity between terminal (M08) 32 of the cluster harness
side connector and terminal 26 of ESP HECU harness side.
Check for continuity between terminal (M08) 33 of the cluster harness
side connector and terminal 14 of ESP HECU harness side.
|
3. |
Is resistance within specification?

|
▶ Repair short
of wiring between terminal 26, 14 of ESP HECU harness connector
and ABS warning lamp module.
|

|
▶ Repair open of
wiring between terminal 26, 14 of ESP HECU harness connector and
ABS warning lamp module.
|
|

Detecting condition
Trouble Symptoms
|
Possible Cause
|
If the HECU detects trouble, it lights the ABS warning lamp while at the
same time prohibiting ABS control. At this time, the HECU records a DTC
in memory. Even though the normal code is output, the ABS warning lamp remains
ON, then the cause may be probably an open or short in the ABS warning lamp
circuit.
|
– |
Faulty instrument cluster assembly
|
– |
Faulty ABS warning lamp module
|
|
Inspection procedures
Check DTC Output
1. |
Connect the GDS to the 16P data link connector located behind the driver's
side kick panel.
|
2. |
Check the DTC output using GDS.
|
3. |
Is DTC output?

|
▶ Perform the DTC troubleshooting
procedure (Refer to DTC troubleshooting).
|

|
▶ Check the CAN circuit
resistance for ABS warning lamp.
|
|
Check the CAN circuit resistance for ABS warning lamp
1. |
Disconnect the instrument cluster connector (M08) and turn the ignition
switch OFF.
|
2. |
Measure the resistance between terminal (M08) 32 and 33 of the cluster
harness side connector.
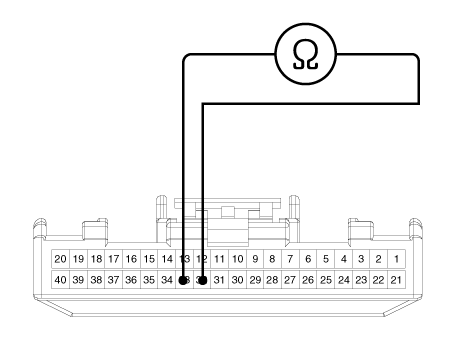
|
3. |
Is resistance within specification?

|
▶ Repair ABS warning
lamp bulb or instrument cluster assembly.
|

|
▶ Check the CAN circuit
wiring for ABS warning lamp.
|
|
Check the CAN circuit wiring for ABS warning lamp
1. |
Disconnect the instrument cluster connector (M08) and ESP HECU connector,
and then turn the ignition switch OFF.
|
2. |
Check for continuity between terminal (M08) 32 of the cluster harness
side connector and terminal 26 of ESP HECU harness side.
Check for continuity between terminal (M08) 33 of the cluster harness
side connector and terminal 14 of ESP HECU harness side.
|
3. |
Is resistance within specification?

|
▶ Repair short of wiring
between terminal 26, 14 of ESP HECU harness connector and ABS warning
lamp module.
|

|
▶ Repair open of wiring
between terminal 26, 14 of ESP HECU harness connector and ABS warning
lamp module.
|
|
Circuit Diagram
Terminal Function
PIN No
Desciption
Current
Max
Min
1
Voltage supply for pump motor
39A
10 MΩ
2
RR EPB motor power
30A
10 MΩ
3
RR EPB motor ground
30A
10 MΩ
4
Clutch stroke sensor signal
-
-
5
Local CAN High
30 mA
-
6
Electric parking brake signal 1
20 mA
250 MΩ
7
Electric parking brake signal 2
20 mA
250 MΩ
8
Electric parking brake signal 3
20 mA
250 MΩ
9
Electric parking brake signal 4
20 mA
250 MΩ
10
-
-
250 MΩ
11
-
-
-
12
RL EPB motor ground
30A
-
13
RL EPB motor power
30A
10 MΩ
14
Ground for solenoid valves and ECU
30A
10 MΩ
15
-
-
10 MΩ
16
-
-
250 MΩ
17
ESP OFF switch signal
16...
Components and components location
Components
1. Front - right (FR)
2. Rear - left (RL)
3. Rear - right (RR)
4. Front - left (FL)
5...
Other information:
Repair procedures
Removal
1.
Turn ignition switch OFF and disconnect the negative (-) battery cable.
2.
Remove the under cover.
(Refer to Engine Mechanical System - "Engine Room Under Cover")
3...
Repair procedures
Removal
1.
Disconnect the negative (-) battery terminal.
2.
Remove the glove box housing.
(Refer to Body - "Glove Box Housing Cover")
3...